Crucial Pipeline Welding Assessment Tips for Quality Guarantee
How can one assure the high quality of these welds that attach the pipeline areas? By comprehending the important pipe welding examination suggestions, professionals can avert possible hazards, decrease pricey fixings, and support the dependability of these vital frameworks.
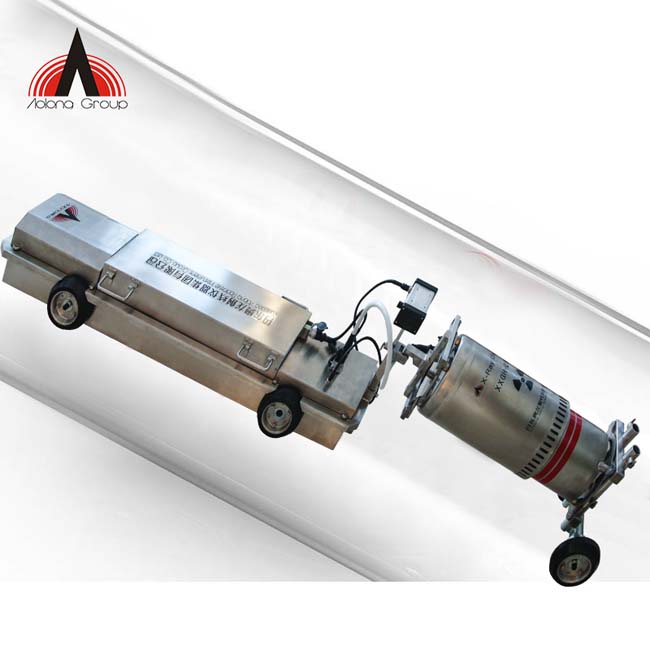
Relevance of Welding Examination
Welding assessment plays a crucial role in making certain the architectural integrity and safety of pipe systems. By meticulously taking a look at welds, examiners can identify any type of flaws or imperfections that could compromise the stability of the pipe. These examinations are essential for preventing leaks, ruptures, and various other possibly tragic failings that could lead to ecological damage, financial losses, and even death.
The value of welding examination can not be overstated, as the top quality of welds straight impacts the general performance and durability of the pipe. Via non-destructive testing techniques such as aesthetic examination, ultrasonic testing, radiography, and magnetic particle screening, inspectors can find imperfections that might not show up to the nude eye. By recognizing and dealing with these concerns early, welding inspection aids to ensure that pipes fulfill market criteria and governing demands.
Inevitably, welding evaluation is a crucial element of quality control in pipe repair service, upkeep, and building and construction (Pipeline Welding Inspection). By promoting rigorous inspection standards, industry specialists can minimize dangers and promote the safety and dependability of pipeline systems
Common Welding Problems
Amongst the difficulties encountered in pipeline welding, usual problems can substantially affect the architectural stability and performance of the bonded joints. Fractures in the weld can circulate over time, jeopardizing the architectural stability of the pipeline. Detecting and dealing with these usual issues with extensive examination and quality control processes are crucial for making certain the reliability and safety of pipeline welds.
Inspection Methods for Pipelines


Non-destructive screening (NDT) strategies such as radiographic testing, ultrasonic testing, magnetic bit testing, and fluid penetrant screening are typically used in pipe welding assessment. Visual evaluation is also important in pipeline welding to determine any type of noticeable defects or gaps. Furthermore, computerized examination techniques using sophisticated technologies like robotics and drones are progressively being employed to improve the effectiveness and accuracy of pipe assessments.
Ensuring Quality Control Specifications
To support rigid high quality assurance requirements in pipeline construction, meticulous adherence to developed market methods and guidelines is important. Quality guarantee in welding procedures requires a comprehensive approach incorporating various phases of pipeline construction. Implementing a robust top quality monitoring system that consists of routine audits and testimonials can additionally improve the total top quality assurance criteria in pipe welding.
Avoiding Pricey Repair Work
Offered the vital value of preserving rigorous high quality assurance standards in pipeline building and Read Full Report construction, a positive technique to avoid pricey fixings is necessary. By carrying out thorough assessment protocols throughout the welding process, potential issues can be identified and corrected at an early stage, inevitably saving both time and money. One crucial facet of preventing expensive repair services is ensuring that welders are correctly educated and certified, as this dramatically decreases the possibility of malfunctioning welds that might cause future failings. Furthermore, utilizing advanced assessment methods such as non-destructive screening can help spot any issues or incongruities in the welds before they escalate right into major troubles. pop over to this web-site Routine upkeep checks and tracking of environmental variables that can affect the integrity of the pipe are additionally crucial in stopping costly repair work. By buying preventative measures and focusing on quality assurance at every phase of the pipe welding procedure, business can reduce the risk of costly repair work and ensure the lasting integrity of their infrastructure.
Verdict
Finally, adherence to appropriate welding examination strategies is important for ensuring the quality and integrity of pipelines. By identifying common welding problems and applying detailed assessment procedures, costly he has a good point repairs can be stopped, and quality guarantee standards can be satisfied - Pipeline Welding Inspection. It is essential for pipe welders to prioritize inspection procedures to preserve the safety and security and reliability of the infrastructure they are functioning on
The significance of welding assessment can not be overemphasized, as the high quality of welds directly affects the total performance and durability of the pipe. Non-destructive testing (NDT) strategies such as radiographic testing, ultrasonic screening, magnetic fragment testing, and fluid penetrant testing are typically utilized in pipeline welding assessment. Aesthetic evaluation is likewise crucial in pipeline welding to recognize any noticeable problems or gaps. Furthermore, computerized inspection methods making use of advanced technologies like drones and robotics are progressively being employed to boost the effectiveness and precision of pipeline evaluations.In conclusion, adherence to correct welding examination techniques is vital for making sure the top quality and integrity of pipelines.